Plate and film Cameras
Plate and film Cameras
Battersea Power Station 1955
Battersea Power Station 1955
Battersea Power Station 1955
Cars
Cars
Battersea Power Station 1955
3D Printing
3D Printing
3D Printing
Geological Museum 1975
Geological Museum 1975
Adrian's Memories
Mechanical Engineering
Mechanical engineering is something that has been an essential component of my life.
As a small boy I always wanted to make things, like a crystal set on my bike at the age of 8.
I soon found out only so much can be done with a hammer, saw, vice, plane and files, but it was enough to get me started and I made all sorts of boxes and cases.
After WW2 it was difficult to get any suitable materials - wood or metal to make things from but luckily my father worked for Twinlock, a loose leaf book manufacturer and often had samples of books with posh hard plastic covers (ebonite) which came in very handy for making front panels. Locally there were 'dumps' where DeHaviland aircraft factory disposed of unwanted ex war equipment which we often visited and took lots of radio chassis stuff home to strip for nuts and bolts and metal.
I remember a local shop had a large sack outside full of round circles of plywood, about 4" diameter, obviously the cut outs from lightening aircraft framework. It had the price 2 shillings and sixcpence on it.
My brother and I pestered our Dad until he grudgingly bought it for us.
It became the material used in almost everything we built for a couple of years.

Photo shows on the left the test meter made when I was about 12 out of a Twinlock book cover for a front panel and a wooden case. The meter and switches were all from the DeHaviland dump and I worked out the circuit myself with a bit of help from Stan Weller who taught me lots about electronics.
To the right is a transistor tester with a sloping front panel I devised to be able to get the optimum bias conditions.
During the printer's strike of 1959 I joined a camera repair firm in Sutton called Garretts. It was run by Harry and his 2 sons Dennis and another whose name I've forgotten after 60 years. I was given all the box cameras to repair and then moved on to Agfa Silettes and other similar types.
One of the jobs always cropping up was to make new eye cups for binoculars that had been dropped by the racing fraternity. We had 2 lathes, one a vintage treadle and the other a Myford Seven.
Harry was a master of the treadle lathe and could turn up an eye cup in about 30 minutes including cutting the inner thread so it screwed on OK. All measurements by eye and all turned with hand held tools and the thread made with a hand thread chaser.
I often had to make up bits and pieces and was allowed to use the Myford after a couple of short lessons.
When the printers strike ended Maynard Studios started up again and I rejoined them as a photographer, but kept in touch with the camera repairers.
A year or so later they contacted me saying they were going to buy a new lathe and was I interested in the old one for £25, which I jumped at.
By now we were living in Ashley Avenue in Epsom and I set it up in the garage. I had just bought the Hassleblad 1000f so one of my first projects was to make some adaptors to fit other lenses to it.
The tricky bit was the bayonet fitting used. It was 1/3 of a turn of a 3 start thread and was a head scratching problem until it dawned on me how it was done - so east really. A friend of Jon's made the first one as he was a real engineer and I made the second as I needed 2 lenses

The large lens is a f5.5 16 inch (400mm) Hugo Meyer Gorlitz and the smaller one is a 15cm Dagor.
The 16" was used to take the air crash photos - see Bits and Pieces

This mechanical equipment lasted until I became self employed and won the contract with the Geological Museum in 1976. Now there was lots more profitable work coming in. The audio visual market was demanding more equipment. One of the earliest was for special 'tracking panorama' projectors which needed special film gates and film drive sproket assemblies to be designed and made.
The tracking panorama projector for Abu Dhabi

The FB2 set up in the old workshop in 1975.
No digital readout in those days, you just kept count of the number of turns on the wheels
So I had to buy a milling machine. The one I chose was an Italian Emco FB2. This was about the biggest I had room for and complete with machine vice and dividing head cost around £1500 in 1975.
About this time I met up with Ron Blackall, a very talented precision engineer who was happy to teach me lots and lots about milling and engineering generally.
Now came the need for making more professional sheet metal work. I bought a treadle guillotine wit a 600 mm cut handling aluminium up to 2mm thick.
I could not afford a bending machine so I designed my own. A good friend Neil Sargent cut up the thick steel and another good friend Bill Haylor welded the bits together. I'm surprised how successful it was for making chassis and cases up to 300 mm wide. I used it for many years.

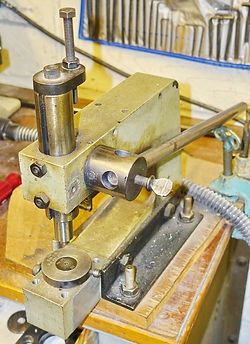

I bought a toggle press for punching holes and bending sheet metal, only short bends up to 150 mm but extremely accurate (+- .1 mm) and with stops so repeatable work could be done. Over the years I have bought all sorts of attachments for it (nibblers, piercers and multi hole punches for cable connectors etc).

I converted a verneer slide gauge into a height gauge.
The equipment stayed much the same until the house extension was finished in 1983 when the new garage became the mechanical workshop, I updated the Emco mill and the Myford to newer models. I inherited a bigger guillotine from Ron Lucking and bought a bigger bender / roller and a new bandsaw. That was all in the mid 80's and very little has changed since except it has all got 40 years of grime on it now as you can see from these recent photos,
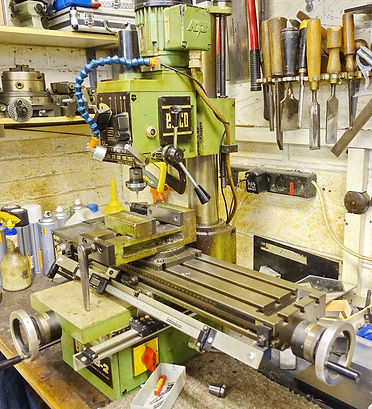
The Emco Mill now fitted with digital read out

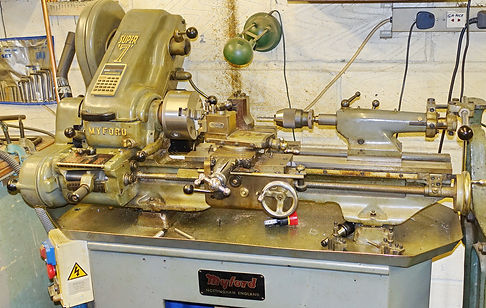
Myford Super 7 lathe, bought new in 1984
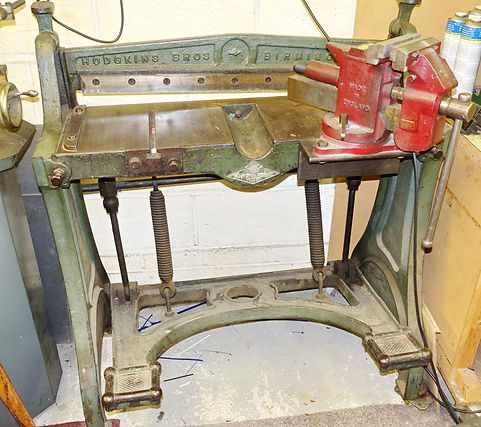
Warco 24" bender/roller /guillotine

750 mm guillotine and vice
safety guard removed for fine work
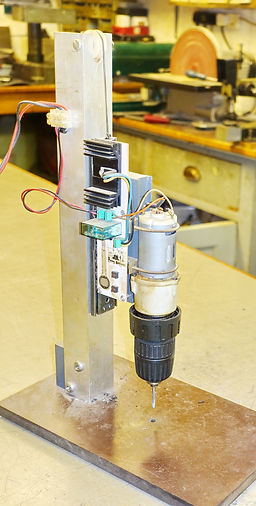
Tapping machine for small threads up to 5 mm. Designed around an old battery drill with special control electronics including a pressure sensitive pad for power and speed.
Made in the 90's it has tapped thousands of holes
Bandsaw with 15" throat and 9" high cut